El cerebro de la fábrica
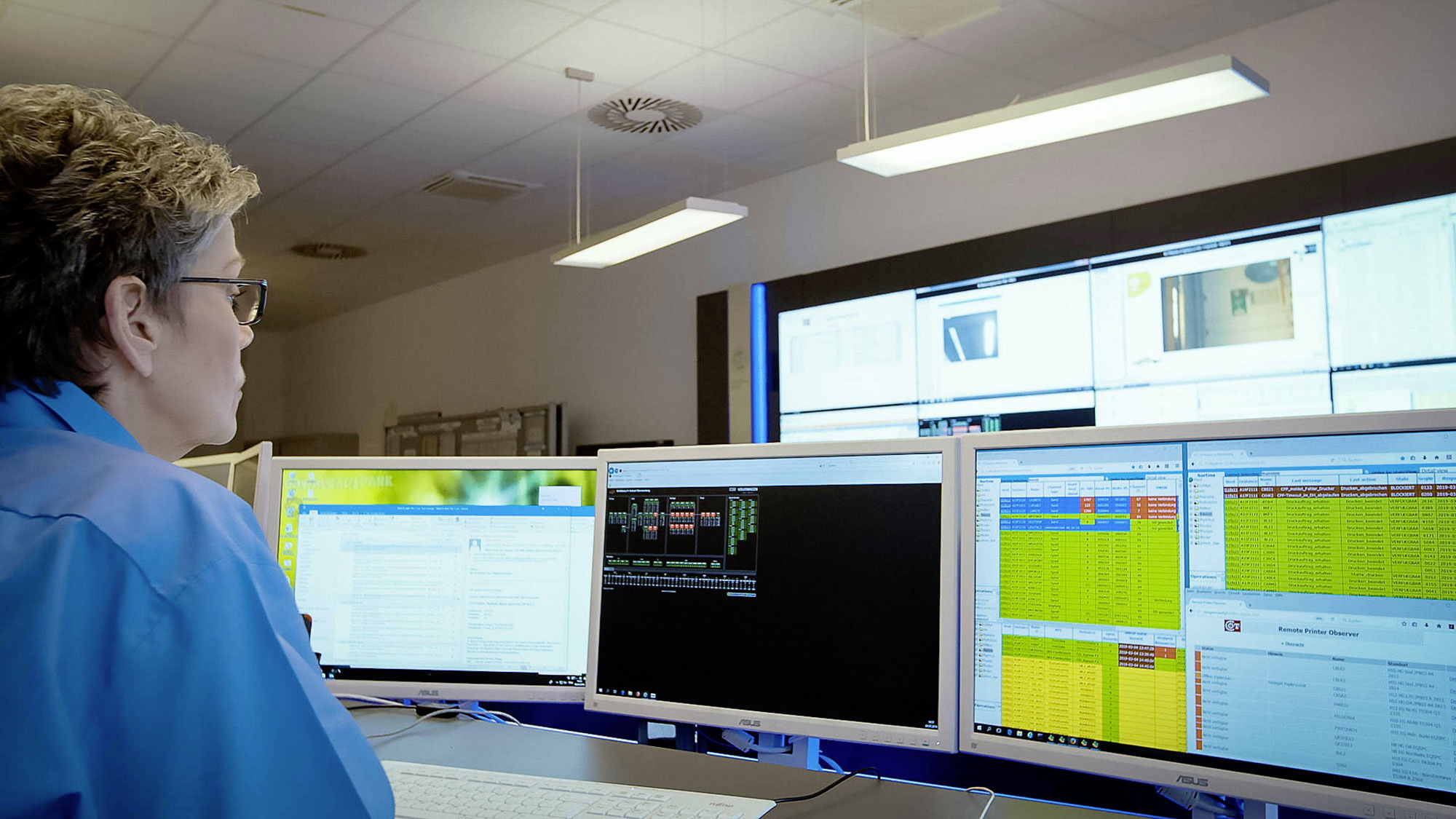
La producción de un auto es una labor compleja. Se deben armonizar miles de variables que influyen en el proceso. El sistema de producción, información y control conocido como "FIS" (que se explica más adelante). Observamos detrás de bastidores del FIS en Wolfsburg, donde cada segundo cuenta para los 3,500 autos que se arman cada día.
Se requieren 200 metros cuadrados, 15 miembros del personal por turno, 50 expertos en total. A esto se deben agregar 16 grandes pantallas, 40 monitores de escritorio, todo tipo de software e incluso más inteligencia del sistema. Y esto funciona 24/7. Y, por supuesto, todo esto se realiza con un estricto control de acceso. No hay duda: aquí en la planta más grande de Volkswagen en Wolfsburg, en la entrada 54, en el segundo piso, se encuentra el corazón de la producción. Ésta es la sala de control FIS, o el “cerebro de la fábrica”. FIS son las siglas de “Fertigungs-, Informations- und Steuerungssystem”, o Sistema de Producción, Información y Control. Este nombre, bastante críptico, abarca todo, desde el hardware modular y el intrincado software, hasta décadas de experiencia y conocimiento especializado adquiridos por los empleados que planean, informan, monitorean y, sobre todo, controlan eficazmente el proceso completo de la producción automotriz.
Empieza tan pronto como el cliente firma el contrato
“Distinguimos entre el proceso del pedido del cliente y el proceso de creación del producto”, explica André Renner, Director de Control de Producción y Planeación de Programas. “Nosotros, el equipo de control de la fábrica y planeación de programas, apoyamos el proceso del pedido del cliente y aseguramos que los autos de los clientes se produzcan a tiempo del lado de la fábrica”. Primero, los clientes configuran sus vehículos con base en muchas variables y firman el contrato del pedido en la distribuidora. Después, la fábrica accede a éste desde la base de datos de ventas.
Antes de que un pedido realmente se concrete en la fábrica, el proceso de pedidos del cliente se verifica con anticipación: ¿Cómo se pueden coordinar los componentes necesarios para el auto configurado con la capacidad de las instalaciones de producción y las entregas de los proveedores? ¿Hay demandas de mercado especiales que deriven en restricciones de asignación o implementación en ciertos sitios? ¿En qué medida se deben considerar las rutas de transporte de suministros y también la ruta de entrega final al cliente? Estos factores y otros criterios similares determinarán la fecha límite de producción vinculante y después la fecha de entrega.
Una vez que se completa esta parte del proceso, se genera algo llamado una “sonata”. Éste es un acrónimo para la frase alemana “Soll nach Tagen” (digamos: “objetivo en días”). Exactamente con cuatro semanas de anticipación, la sonata desglosa la capacidad de la línea de ensamblado en la fábrica en cuestión, en este caso Wolfsburg. La planeación es precisa. Por ejemplo, la línea de ensamblado corre con un intervalo de 60 segundos. Pero debido a que se requieren 73 segundos para instalar un quemacocos, los autos con esta especificación se deben mezclar con otros autos en la línea. Ésta es la única forma de compensar los segundos adicionales que se requieren. Nunca se producirán diez autos con quemacocos de forma sucesiva. Y el quemacocos es apenas un ejemplo de los cientos de especificaciones que se deben tomar en cuenta de manera precisa. Como observa Renner, “Con más de 60,000 vehículos fabricados por mes, un auto normalmente no compensa al 100% por otro, excepto en el caso de pedidos de flotillas a gran escala”.
Posterior a esta planeación precisa, inicia el proceso de creación del producto. Por ejemplo, en la primera etapa de desarrollo, se genera una lista de partes para cada vehículo y después se cambia en el caso de una actualización del modelo. “La lista de partes es la base para el matrimonio entre el pedido del cliente y la logística de los componentes”, explica Renner. A partir de aquí no hay retorno. El FIS asigna a la sonata un número de ID único para ese auto en particular. Ésta contiene la fecha de producción exacta para este vehículo. Al mismo tiempo, todos los proveedores reciben la lista de componentes requeridos para ese auto.
Ahora puede comenzar la producción
Cuando llega la fecha de producción, se fabrica el vehículo. “Nuestros trabajadores de ensamblado se deben concentrar únicamente en conjuntar las partes del vehículo”, afirma Hilmar Schimenas, que dirige la sala de control automotriz FIS. “Por esta razón debemos darles las mejores condiciones para ellos y traducir el pedido del cliente a un lenguaje de producción, por decirlo, así, utilizando el FIS. Las personas, la maquinaria y los materiales deben estar coordinados con precisión entre todos”. Aquí pueden ocurrir bastantes cosas: los proveedores tanto internos como externos podrían tener cuellos de botella para la entrega, las máquinas se podrían descomponer, las personas se pueden enfermar, las fuerzas de la naturaleza pueden interrumpir la producción. “Registramos cada alteración individual en la cadena del proceso, desde los proveedores hasta la producción, para cada instalación. Si ocurre un problema en una de las cuatro líneas de ensamblado, actuamos inmediatamente”, dice Schimenas. El objetivo es claro, no se puede perder un minuto del tiempo de producción y las líneas deben funcionar lo más ágilmente posible en cada turno.
Como esta tarde a principios de marzo, donde la producción en Wolfsburg funciona como un mecanismo de relojería. Una impresora o un escáner de partes podría dejar de funcionar, pero el equipo lo arregla rápidamente. “Aquí hemos visto prácticamente cualquier cosa”, dice Schimenas. “Pero de alguna manera, siempre logramos solucionar cada problema y volver a avanzar”.
Wolfsburg ha tenido el FIS desde 1992. Desde ese momento hasta mediados de marzo de 2019, han salido de sus líneas más de 18 millones de vehículos, con un índice actual de 3,500 autos por día.
La plataforma FIS modular y la sala de control de la fábrica no sólo se encuentran en la planta de Wolfsburg, sino también en más de 40 fábricas del Grupo Volkswagen, alrededor del mundo. La estructura modular del FIS permite lograr esto eficazmente debido a que los módulos se pueden adaptar de modo flexible dependiendo de la situación en cada planta. Si Wolfsburg tiene cuatro líneas de ensamblado, pero Dresden sólo una, eso no representa un problema para FIS. También se requiere flexibilidad porque las plantas tienen diferentes grados de automatización, así como otros procesos de producción. Pero todo esto es posible para FIS, pues se pueden integrar nuevos módulos sin tener que reescribir el software general cada vez.
El Grupo Volkswagen ya ha producido más de 50 millones de vehículos en más de 20 años con el FIS. En éste se han escrito más de doce millones de líneas de código de programación – casi una cuarta parte de lo que tiene Windows – para 280 versiones de modelos. Más de 200,000 empleados de producción en el Grupo trabajan con FIS cada día. Y el sistema registra más de 1,000 piezas de datos para cada auto.
¿Qué hay en el futuro para FIS? “Deseamos ampliar el sistema con inteligencia artificial de tal forma que éste pueda controlar la producción de forma autónoma”, comenta Renner. Se pueden añadir funciones individualizadas para cada planta o fábrica y tener un acceso discreto con la ayuda de la tecnología de aplicaciones. Los miembros del equipo FIS en todos los países ya están en contacto directo unos con otros para compartir su experiencia y poner en práctica esta visión.
Muchos expertos de las plantas alrededor del mundo dicen que en Wolfsburg, el Grupo Volkswagen desarrolló el sistema de control de fábrica informático más ampliamente estandarizado. Algunos incluso dicen que es el mejor.
